Powering the Industrial Metaverse
3dverse is at the forefront of the industrial metaverse - an emerging concept that represents the next frontier in digital transformation. It is a virtual representation of the physical world, where real-time data from sensors, machines, and other sources is used to create a realistic, dynamic, interactive, and immersive environment.
Festo Metaverse Experience
Festo partnered with 3dverse to create the "Festo Metaverse Experience," an immersive virtual showroom featuring the digital twin of the MPS 403, one of its flagship products.
Connect AI and API to digital twin
Real-time collaboration and multi-user training
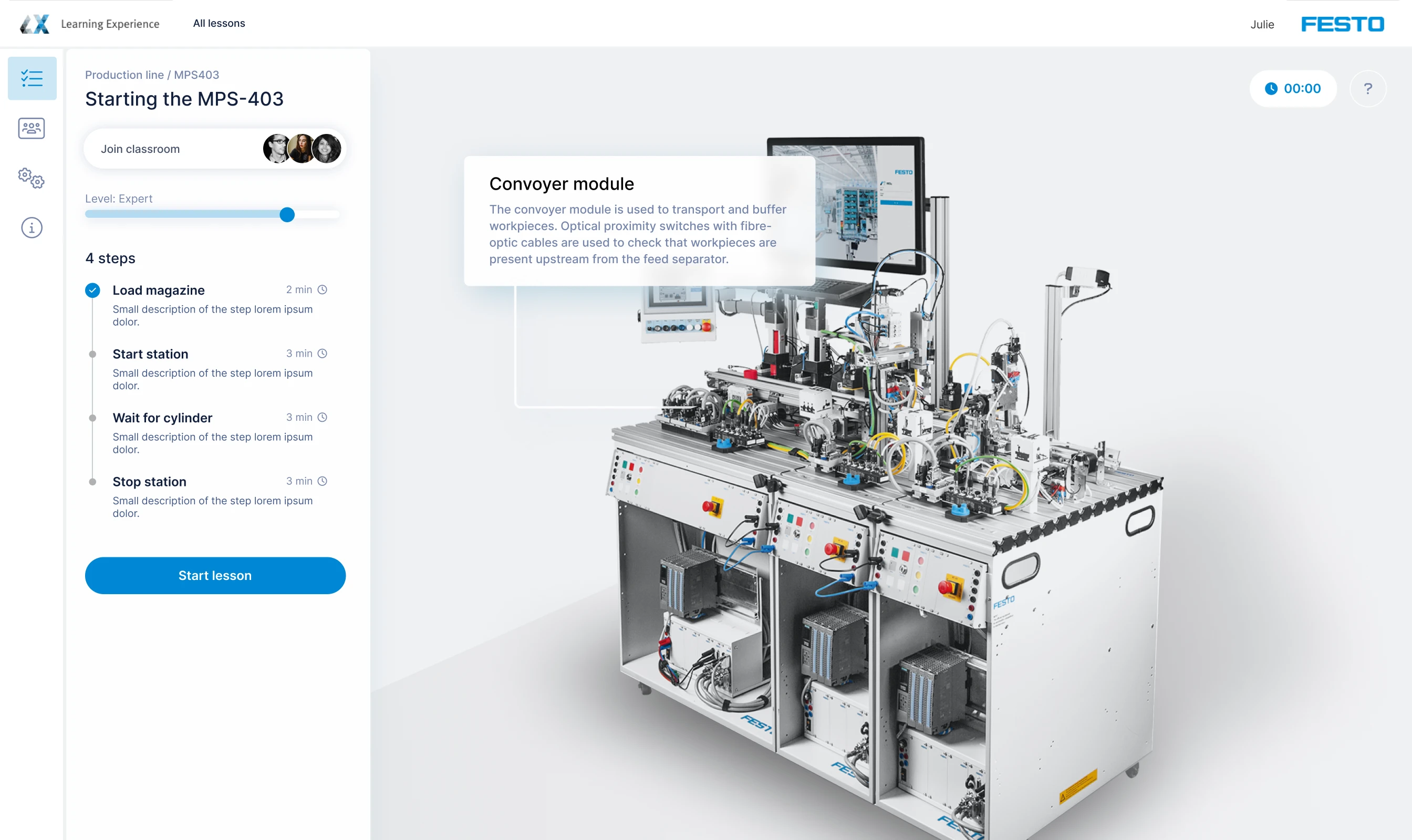
Predictive Maintenance
Facilitate effective training by simulating error scenarios, allowing safe practice of diagnostic and corrective procedures.
Interoperability & Connection
Provides an accurate, real-time view of machine operations by synchronizing the digital twin directly with physical sensor feeds.
High Performance & Cross-Platform
Delivers complex simulations with low latency and high performance across desktop, mobile, VR, and AR interfaces.
Prototyping an Immersive Digital Learning Platform
To test the feasibility and effectiveness of digitizing practical work instructions, initially in Word format, for integration into an immersive 3D environment to improve learning and training.
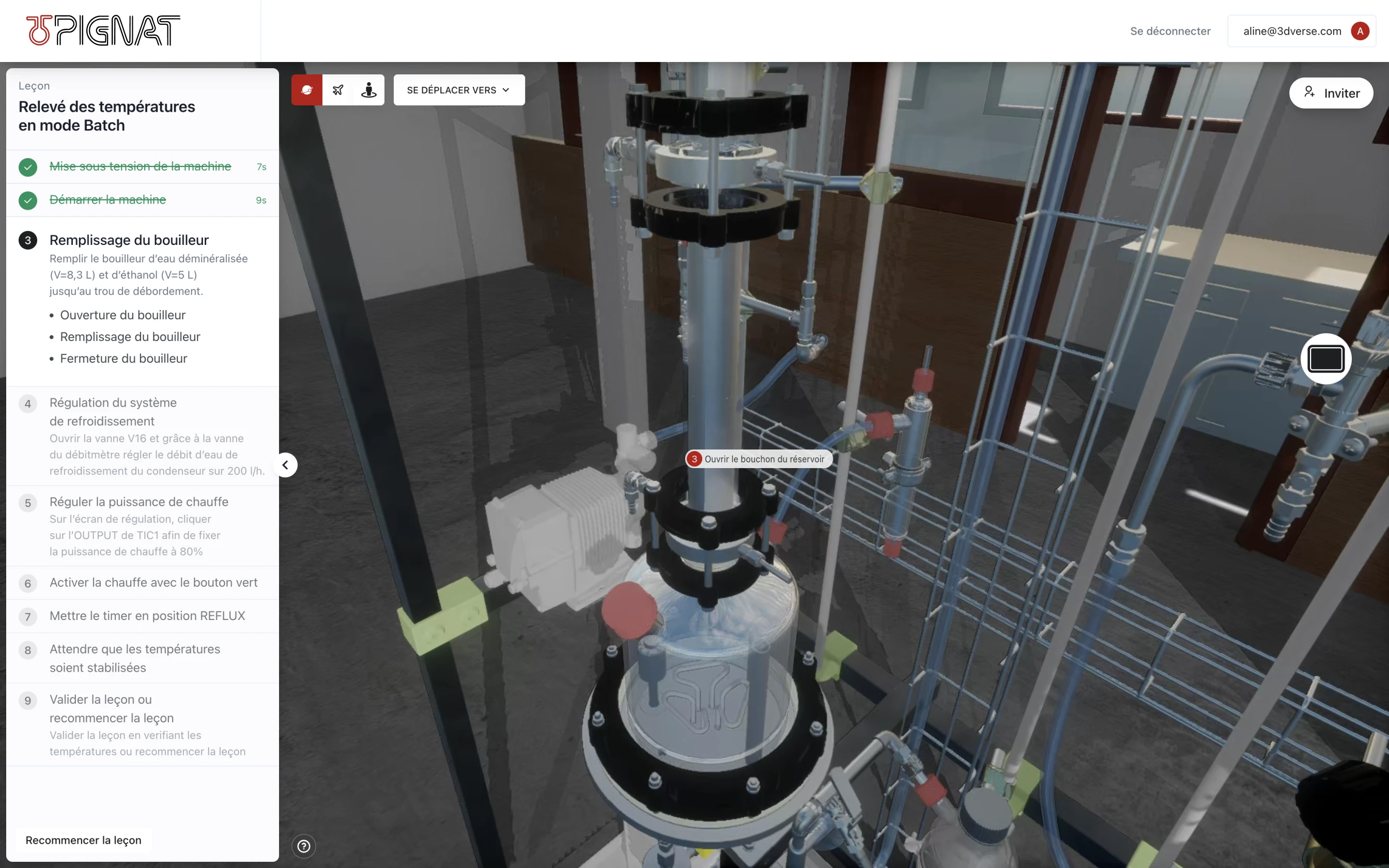
Training Module
An immersive 3D environment reproducing a DVI 3000 machine and its surroundings.
Virtual Control interface
A functional replica of the control interface to manipulate virtual controls and observe real-time machine reactions.
Interactive Guide
A step-by-step guide integrated into the platform to support users in learning operating procedures.
The Alten Story
By replacing traditional static designs with dynamic and interactive simulations, this technology enables industry professionals to work with 3D models connected in real time to the physical factory.
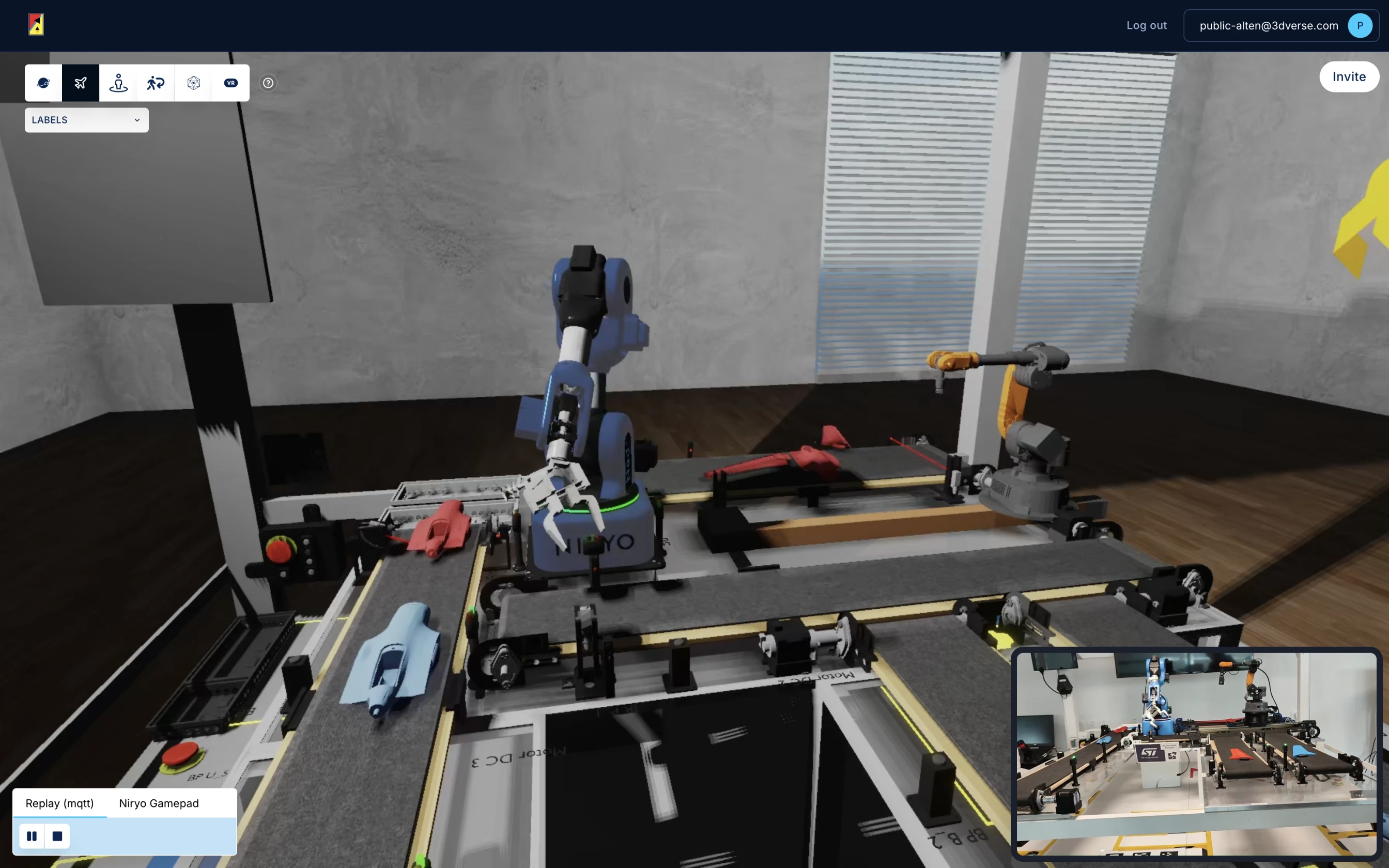
MQTT Protocols
Leveraging MQTT and OPC UA protocols, 3dverse ensures seamless interoperability and scalability.
Immersive training
Facilitates collaboration between humans and machines through seamless real-time connectivity between the real and virtual worlds
Digital twin Architecture
By replacing traditional static designs with dynamic and interactive simulations, this technology enables industry professionals to work with 3D models connected in real time to the physical factory