Festo Metaverse Experience
Festo partnered with 3dverse to create the "Festo Metaverse Experience," an immersive virtual showroom featuring the digital twin of the MPS 403, one of its flagship products.
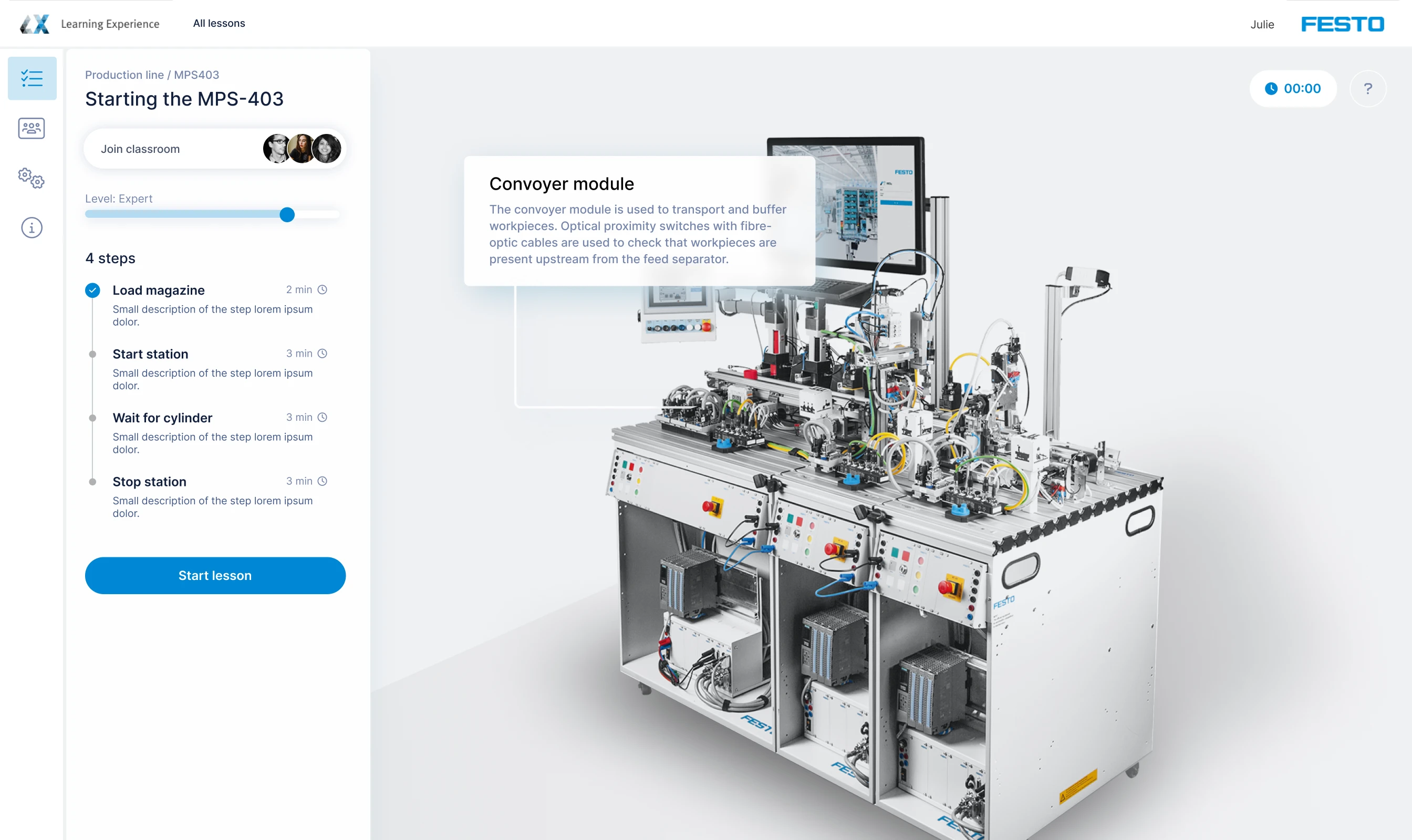
Industry 4.0 Demands a New Approach to Workforce Training
As Industry 4.0 accelerates—with its integration of IoT, robotics, and advanced automation—industrial companies face an urgent need to upskill their workforce. Traditional training methods often fall short when it comes to safety, cost-efficiency, and engagement. To address these challenges, companies must embrace new, scalable learning solutions.
Festo Leads with Immersive Learning Through the Metaverse
Festo, a global leader in industrial automation and technical education, is redefining technical training by leveraging the power of the metaverse. Their objective: make industrial training more engaging, accessible, and cost-effective, while minimizing risks associated with operating complex physical machinery
A Virtual Training Environment Powered by the 3dverse OS
To realize this vision, Festo partnered with 3dverse to create the "Festo Metaverse Experience," an immersive virtual showroom featuring the digital twin of the MPS 403, one of its flagship products.
Our collaboration with 3dverse has allowed us to explore the full potential of the metaverse for technical training. Thus, Festo Metaverse Experience offers immersive and collaborative learning opportunities, reinforcing our vision of accessible and interactive training for the industry.
Christophe Perez - Head of Software Application Engineer, Festo
Accessible from any device (computer, mobile, VR, AR, etc.), the 3dverse platform has allowed Festo to create a unique learning experience, combining the physical and virtual worlds. This project demonstrates several key concepts:
Remote training and collaboration: The virtual classroom allows for interactive, multi-user training in real-time.
Interoperability: The 3dverse architecture allows the MPS 403 machine to be connected via an API. The digital twin, synchronized with real-time data from physical sensors, offers users a faithful representation of the machine's operation.
Pedagogy: Programs can be tested before implementation on the machines, with real-time 3D visualization, allowing for problem identification and simulation of adjustments to optimize production.
Predictive maintenance and simulation: The digital twin allows the simulation of breakdowns and errors to train learners to correct them. The simulations operate with low latency and high performance, regardless of the device used (desktop, mobile, VR, AR).
Conclusion: Training the Industry 4.0 Workforce in the Metaverse
By combining an immersive virtual environment with an interactive digital twin, Festo offers a unique learning experience that transcends the limits of the physical world. Thanks to the 3dverse platform, training becomes more accessible, flexible, and efficient, preparing the workforce of tomorrow for the challenges of Industry 4.0.
Demo